What Is Embossing? | Everything You Need To Know About Embossing!
- Andy Lau
- Apr 3, 2022
- 5 min read
Updated: Oct 31, 2024
Table of Contents
Nothing makes meticulous texture quite like embossing!
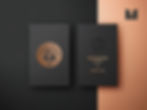
Have you ever seen the classic chocolate packaging with a company logo embossed on the top? Well, this article is all about these arts and how they are made by embossing.
Embossing is a technique that has been around for centuries. The technology behind it is simple yet very effective. It's the act of pressing paper or cardstock between two heated dies to create an impression of the design on the paper.
The introduction of embossed packaging is a worldwide trend that has quickly spread. This technique has the perfect balance of modernism and elegance, making it a hit in almost everything.
What is Embossing?
The word "emboss" means to create a raised surface from pressure or heat. Correspondingly, embossing is the process of creating raised surfaces in paper or other materials by applying pressure.
It is often used to decorate the covers of books and other items with a design or pattern. Embossing can be achieved by using letterpress printing, with a mold pressed into paper, or engraving tools to cut away from the surface.
The ancient Egyptians developed the process of embossing and used it on papyrus documents to create a raised design.
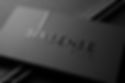
It can be done by hand, but it is more commonly done using an embossing machine. The machine presses the material against a die, which creates the design on the material's surface.
Embossing and emboss printings add dimension to a surface and enhances its appearance. It also protects against wear and tear. Embossing can be used to get attention in a crowded market, as it is an excellent way to brand a product or package with your company's logo or name.
What are the Benefits of Embossing?
Embossing provides many benefits to your cards and other products or packages, such as adding texture and dimension to the finished product. It also makes it easier for people (especially blinds) to read what's written on the card or paper because embossed letters are raised above the material's surface.
Besides that, embossing offers the following benefits:
It makes your packaging more fun and better-looking!
Embossing creates a textured look to your product's packages and gives a "handmade" feel!
It makes your cards more memorable and unique!
It attracts attention and ultimately influences the rate of product sales!
Embossing conveys high-quality contrast with possibly everything.
It is traditionally a way of making foil/paper printing easier.
How is Embossing Done - The Process
An embossed design is something that anyone can do. All you need are the proper tools for the task! It can be professionally done with modern equipment, or it can be conducted at home.
On a professional standard, embossing is done as follows:
Step 1: Make the Dies
To make embossing work, you need two dies customized with the desired design.
The pattern on the first die (generally known as the male die) is elevated on top. In contrast, the pattern on the second die (the female die) is recessed into the surface.
Dies are available in various styles and materials, including magnesium, copper, and brass. The one that's utilized essentially relies on the ideal final appearance.
Step 2: Enter the Dies
The dies are then loaded into a massive press that can be any of the following:
Clamshell: The sample is sandwiched between the press's two halves.
Straight stamp: The sample is inserted into the press and gets out to the other side
Roll: The sample is transmitted through rollers where it's embossed with the layout
Step 3: Press the Sample
The press may reach temperatures of up to 200°F; however, it is lower normally. The sample that is getting embossed is then squeezed between the two plates of the die.
The embossed design looks fantastic on the sample now. The method explained above is for mass production used by most manufacturers.

Even though embossing appears to be quite deep, it is usually no deeper than 15 microns and a maximum of up to 25 microns. That's a quarter-millionth of an inch.
The typical embossing is around 1/64th of an inch in size. You can see how the depth of a die impacts the shape of the final product. It's worth noting that as the depth of the die grows, so does the likelihood of the paper ripping.
Presses that perform embossing and presses that handle foiling are, for the most part, comparable.
Both techniques need a great deal of pressure and, in some cases, a preheated plate. Furthermore, because foiling and embossing are mostly done concurrently, it stands to reason to have a tool that can do both.
Is Embossing the Inner Paper of Candy Pad Worth It?
Chocolate can be an expensive product, so it's essential to make sure that you package and deliver them in a way that keeps their value.
Embossing the inner paper of candy pads is a great solution as it's both affordable and safe - plus, chocolate always looks good in them. You can customize your candy pads for the specific needs of each customer. Plus, being original and different should be the only way to make your chocolate business stand out.
And this manufacturing process (embossing) comes into play to make custom papers for your candy pads. Most of the candy pads are made of a particular type of glassine paper.
When embossing is done, this paper gets many small balls like spring. This structure gives the candy pad elasticity and cushioning. Moreover, the candy will stay intact and resist breaking while being stored on this paper.
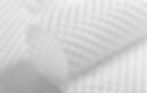
It can protect your chocolates while shipping in a spring-like way with food safety. Ultimately, it certifies that the quality of your products remains intact and allows you to prioritize other aspects of your business, such as customer satisfaction.
These candy pads may also create a better experience for your customers by providing a textured surface that feels good as you bite into it.
Embossing vs. Debossing: Which One Should You Choose?
There are more commonalities than differences when it comes to embossing & debossing.
As mentioned above, embossing is to create a raised design on a surface by pressing it! While debossing is creating a recessed design on a surface by applying pressure with the help of a tool. It creates an impression on the surface and makes it appear as if the design has been pressed into the material.
The contrast between embossing and debossing is that one process creates an illusion of depth on a flat surface. In contrast, the other process creates a raised surface from a flat surface.
So, it's your choice, or better say, your customer's preference of picking one over the other! Both have advantages; thus, it is often a matter of personal preference. Try with both samples to decide which you believe is the best fit for your chocolate packaging.
The Final Verdict
While embossing is more trendy than debossing, both will help your next chocolate packaging's print stand out and add an air of refinement and finesse.
Believe your choice; browse some of our candy pads inspirations and other chocolate packaging designs. There are many reasons to love Michael Package's candy pads. We make custom candy pads in a dust-free environment, ensuring no chance of contamination.
Above all else, ingredients are 100% recyclable with great food safety, so you can rest assured that your chocolate packaging is sustainable and safe for the environment. Contact us when you're ready to start on your next print project!